This article was written by the remarkable Daniel Burton, an inspiring young man living with Asperger’s who has spent years carefully designing his own road-legal race car. The design is now ready for testing and final tweaks before being built.
If you would like to contact Daniel regarding the Burton Trackster and you think you can help, please use the contact form on Silodrome here and we’ll connect you to him.
A Little Bit About Me
Bit of a cliché headline, but it’s true and it was born out of necessity! I happen to have High Functioning Asperger’s and due to the difficulties associated with that I cannot stay employed by a regular company. Luckily, Australia happens to have a welfare program for folks like me.
I am considered disabled by the government, so I get paid a modest sum to look after myself, my wife and my daughter. In between looking for a suitable employer and doing small jobs for my company, Burton’s Tube Worx, I put my versatility and ability to learn very quickly to good use inventing and designing things. I don’t see myself as disabled, I’m just not able to meet the status quo!
I enjoy prototyping and have developed skills and collected equipment to help me with the task. A VR helmet, a DSLR camera for photogrammetry, a Lulzbot Taz6 3D printer, a fast laptop for CAD/FEA/CFD and an old laptop for literature. With this equipment I have managed to develop a whole heap of products. Most need a prototype made, patents sought, testing performed and to be put to manufacture.
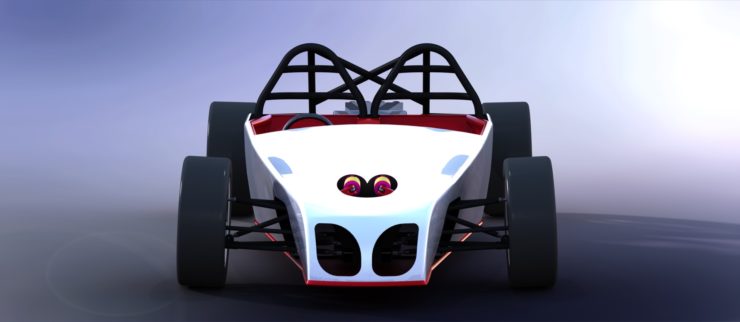
Just a matter of saving enough money or finding an investor or consortium to make them happen. It can be disheartening at times having done so much work and not being able to show people, so when I went to my first hill climb with my dad at Collingrove in the Barossa Valley, I found a new product to work on.
The hill climb was great, dad and I couldn’t stop talking about building a car of some kind. I remember there was quite some conjecture as to what kind. Dad liked the Ariel Atom and Exocet style cars. They typically run a car engine and transmission, and this seemed like a massive waste of weight for a hill climb vehicle. Not only that but the suspension kinematics were compromised by the chassis shape, a two-seater.
I personally liked the Formula Libre cars. Not just because they were the fastest, but the aero and engineering looked much more complex and interesting! Bell cranks, bike engines and chain drives. These cars made sense to me. They were made fit for the purpose of hill climb! My dad on the other hand had passengers in mind. He wanted to be able to scare mum and get sideways. I wanted to go as fast as I could up the hill, I had to make a choice on what path to take.
The Initial Concept
I ended up choosing the Formula Libre cars at first. The crazy aero and the chance to dominate with clever engineering was far too attractive and on top of all that, because my Asperger’s sometimes rules the day, the Libre cars were stuck in my head. So that’s where I began. At that stage I had a few of the needed skills for designing a car. I was a metal fabricator with a basic machining background and with something in the region of 20 years’ experience on different CAD systems, I felt like I had a good starting point for the chassis.
I ended up drawing about 8 different Formula Libre chassis’ before I realised, this was outside the scope of my skills. I was putting lifted noses, ground effect tunnels and all sorts on. Nothing looked how it should! CAD is not like pencil and paper which is guided by art and flow. CAD is driven by math and constraints so I had to tell the program how high that lift should be or how wide and long that tunnel should look. I wasn’t informed enough to make those decisions yet. It is for those reasons I shifted the design over to a two-seater that was less dependent on aero and more about learning instead.
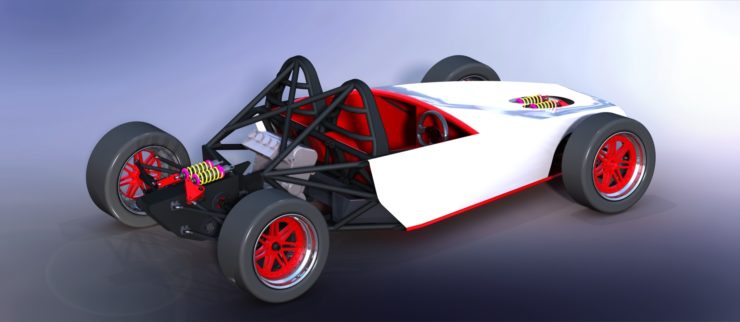
The Learning Process
Something like 80% of the information was still outside my knowledge base and I had no clue where to start. I ended up doing the millennial thing and Googled it! I found a lot of information, too much information actually and most of it was aimed at the layman! This wasn’t going to get me anywhere! I needed hard data from a good source! Race engineering books where the next natural progression, but on my budget, very costly. I would struggle to gather one book every 2 months. That was when I found an online book depository for quite a cheap fee. Full of research papers and books to fill my appetite. It really took off from there.
I began reading while at the same time doing detailed examinations of images related to that area of the car. A picture for my brain, is like a book! I can glean far more information from a picture than I can from a piece of literature. For the average person the writing is the main information and the image is the supplement. For my brain it works backwards. The image is far more useful, and I find them easy to recall. A very handy skill for my chosen line of interests.
I ended up with a bunch of ideas in my head from this cavalcade of information and from all those years of driving and tuning virtual cars. It was gratifying to be able to tell myself that all those years of playing video games and reading magazines in school was paying off. It had informed me quite thoroughly and not much in these technical books came as a surprise to me (except all that algebra).
I was able to verify my understanding of the science behind these racing cars rather than just my assumptions gleaned from unreliable sources. It was at this stage that I began writing down a spec sheet to form the basis of my drawings. It is surprising what can be gleaned from this short list of specifications.
Designing The Supercar Beater – The Burton Trackster
After making this database of cars in the same class as mine, I looked to the rule of thirds (the track width is equal to 2/3 the wheelbase length). It is derived from the golden mean, which is a composition and ratio guideline based on the Fibonacci sequence. The Fibonacci sequence is found all through nature, from a snail’s shell all the way up to a hurricane. This is where art and maths combine, just like in the best car designs.
From my examination of my new database I landed at a wheelbase of 2560mm and a 1705mm track at first. This quickly changed to accommodate the cars modular design and I ended up finishing at a wheelbase length of 2560mm and a track width of around 1850mm. A bit more over-square than I was after but this has the advantage of less load transfer to the outside wheels allowing quicker cornering. It also allows room for a “utilities” tunnel through the centre of the car and room for two large people.
These people can have a maximum 550mm width at the shoulders and a maximum height of 6’6” or 2011mm. The average human is 460mm across the shoulders and only 5’10” or 155mm. Plenty of room for the larger person which is a common gripe. Boutique sports cars are renowned for this problem. Only designing for the 95th percentile. I prefer to have my cake and eat it too. Clever packaging is how this was eventually achieved.
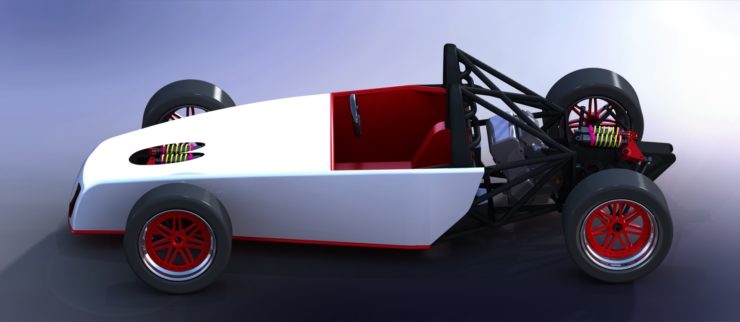
Safety and comfort seem to be an after thought in a good deal of boutique vehicles. It’s an inherent part of some designs and makes them look great but leaves the occupants quite vulnerable in the event of an impact or roll over event. Even though motorsport is inherently dangerous, I felt that safety should not be sacrificed for performance. Far too many deaths have occurred, and lessons learned to ignored them! It would be an insult to the memories of some amazing men and women! This though process has guided the chassis design quite significantly. High chassis sides were a must, along with an internal divider that separates the driver and passenger compartments.
The angle of the occupant’s legs, neck and spine was also looked at. The shape and cushioning used in the seating has a marked effect on the occupant’s injury rate as show by the research paper conducted by Toyota’s WEC racing program. I chose the safest of the options which will likely be adopted in the 2021 WEC regulations. The internal carbon tub that fits inside the chassis is unfinished in the images presented. It will eventually feature a fixed moulded seat that can be tailored to suit each driver with a polyurethane foam seat insert.
This type of seating style is markedly stronger than a separate seat bolted to the chassis and keeps the driver in the optimum zone of safety under the roll over protection system. To adjust for different driver heights the pedals move to your feet on a rail system. This has the added benefit of keeping the weight balance at its optimum point no matter the driver’s weight and height.
The engine and transmission were the next fork in the road. Front? Rear? Middle-front? Middle-rear? North-South? East-West? The typical road to travel in this niche is either the mid-rear mounted East-West route or the mid-front mounted North-South route. Confused? These are all reasonably efficient ways to go for a boutique car, but after much research they all presented draw backs that were not present with a mid-rear mounted North-South configuration. Compromised suspension kinematics, compromised engine placement, driver comfort and weight balance issues were all things that presented themselves. These were all unacceptable to me and drove my choice to the rear mounted North-South configuration!
Choosing The Engine
Realistically this car can use any engine from the family of inline engines. Due to the high availability of GM LS series engines around the world it was the first engine I looked at. They are quite heavy but being a pushrod engine and having a steep V-angle they are compact. That works very well for diffuser tunnel placement and exhaust routing.
I also looked at the Honda K24 crate engine which is a good compromise between weight, power, packaging and availability. The massive unseen downside to the rear mounted North-South configuration is that a transaxle that is also a structural member is upwards of $20,000 AUD. A big kick in the budget. My prototype needed a cheaper way to get drive and power but still retain the ability to use a transaxle for road legal engines when the time comes.
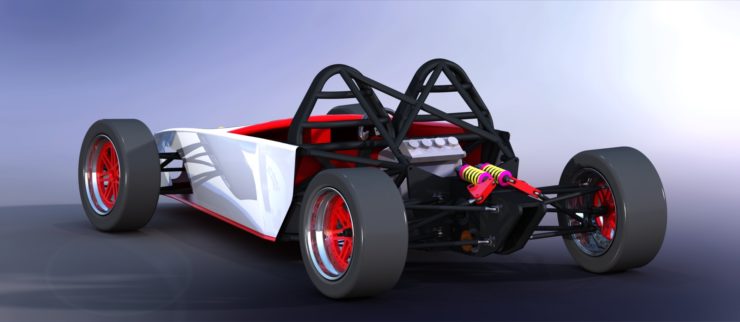
I considered motorcycle engines back when it was to be a Formula Libre car. The inspiration for my idea came from a combination of Formula Libre and Formula 1000. They use a faux transaxle to contain the chain driven differential, the adjustment mechanism for chain tension and all the associated suspension mounts. I designed something very similar to this and mounted it to a torque plate/bulkhead on the rear of the chassis.
To get the packaging I was after I used a double reduction chain drive. The chain tension adjustment comes in the form of a pair of eccentric bearing mounts that rotate the secondary shaft to properly tension both chains at once. This gives room to optimize the suspension kinematics and allows a quick change of the gearing and chain tension from outside the case. By replacing the sprocket sizes up or down you get a different top speed.
The front suspension system was designed last and mounts on a bulkhead. The main reason for using a bulkhead is suspension kinematics. Normally you would design to mount near or on a tube node and attempt to drive your arms from these nodes or points to the wheel upright. These points can only be placed in certain areas before it starts looking weird from a design perspective and terrible from a kinematics perspective. To overcome this problem, I used a bulkhead and suspension mounting frame that bolts to it. This gives me complete freedom to optimise the front suspension to match the rear.
Once I finish the modelling of the vehicle, I need FEA, CFD, and suspension simulations performed on my model. There is a saying I like and feel applies here. Garbage in, Garbage out! I could do these tests myself, but I am not experienced enough to deliver a guaranteed result without correlating to some type of physical testing. A company that has experience in these respective motorsport professions will be needed. The great thing is that I have developed my model so it can change to be optimised easily.
Hopefully costing less in the long run for testing. Suspension kinematics analysis, torsional rigidity and beaming test, FIA ROPS certification and Aero optimisation are all in my sights. When the optimisation is complete, I will need to purchase some quality sim racing gear and upload the model to R Factor 2 to test drive it. This will help to tell me if all the parameters are correct and show that it performs as I expect it too. This will not only be an interesting test of the car but a verification of my design skills. Any flaws in my ideology or that of the testing companies’ skills should show up here.
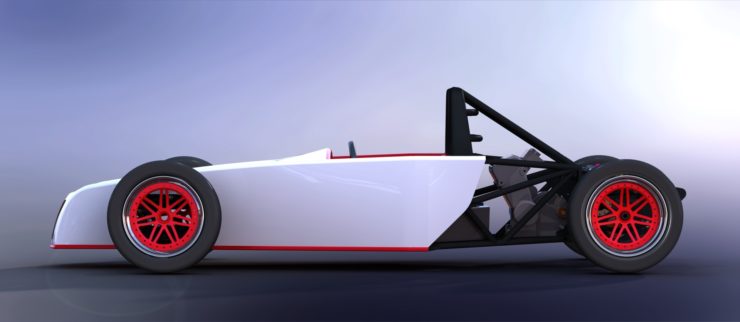
Now a few things that don’t really fit into a paragraph anywhere. How much does the weight balance change when going from the bike engine to the LS engine? It goes rearward from 55% to 60% which is inside the typical range of this type of vehicle. It is also easily returned to 55% with a bit of ballast in the nose of the vehicle. How much does the car change across engine types? The suspension kinematics stay the same from the faux transaxle to the real transaxle.
The radiator configuration is situated in the nose for the bike engine and K24 engine. Side pods are added for the LS engine. Container sizes change for the engine’s ancillaries. A new torque plate and engine cradle. Rebuilt dampers with new springs. Larger discs and callipers. Etc. This entire platform allows a system for cost and skills progression. Increase power, aero or grip at a rate that is comfortable for the driver’s skill set and bank account.
The Future Of The Project
I wish I could give some kind of delivery date. But a lack of money could see this project never leave the ground! I have pushed it as a far as I can with next to nothing. At this stage I really need to find a backer that sees the potential of the car and wants to go into business. The big problem there is that people always want to change your designs intent. It would need to be someone who understands that kind of laser focused thinking. Which I feel is a rare thing. Or I need to win the lottery!
If you would like to contact Daniel regarding the Burton Trackster and you think you can help, please use the contact form on Silodrome here and we’ll connect you to him.
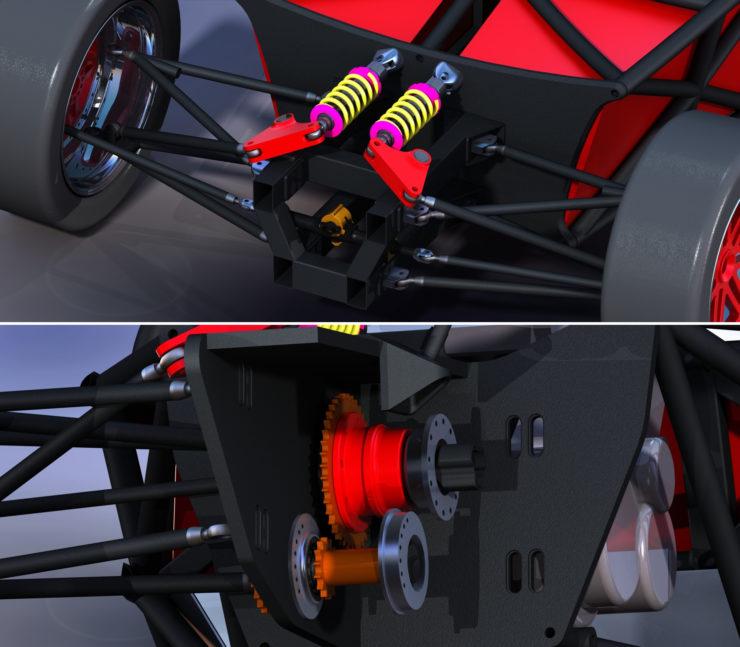
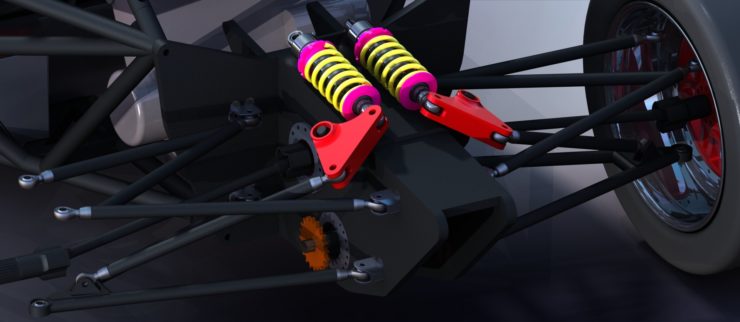
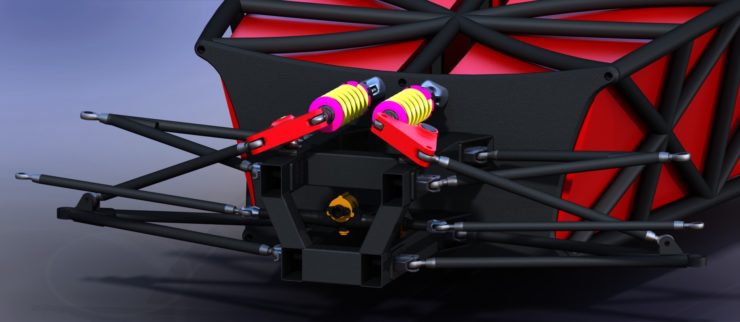
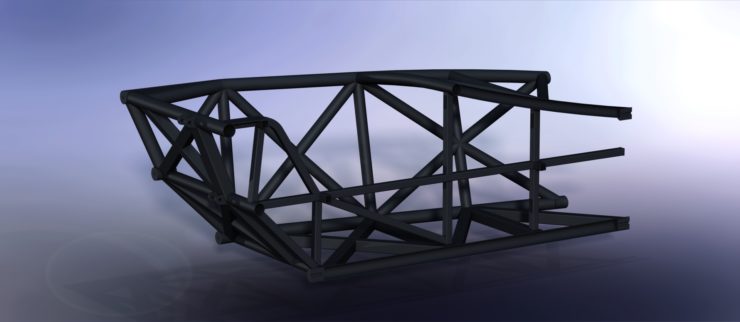
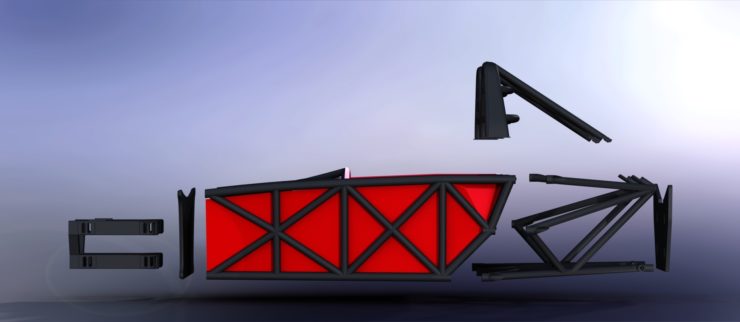
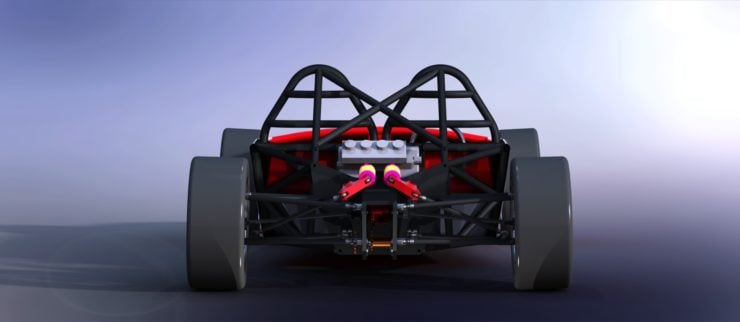
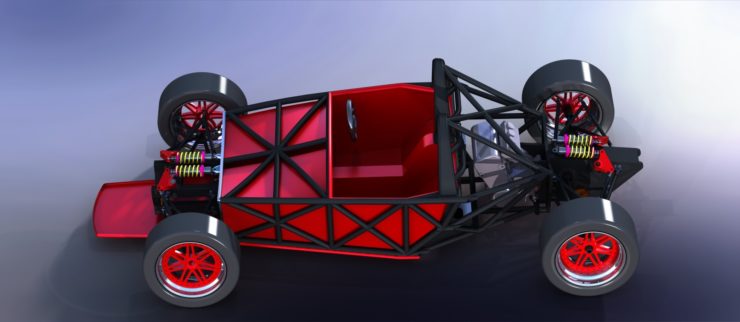
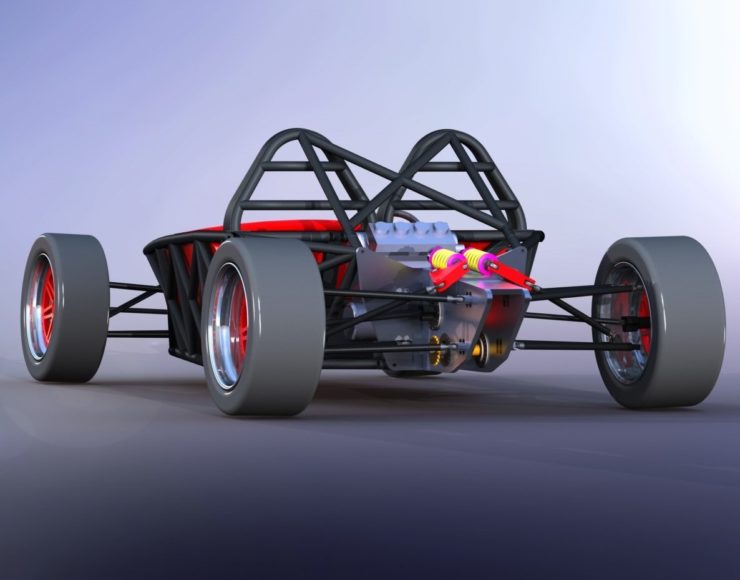
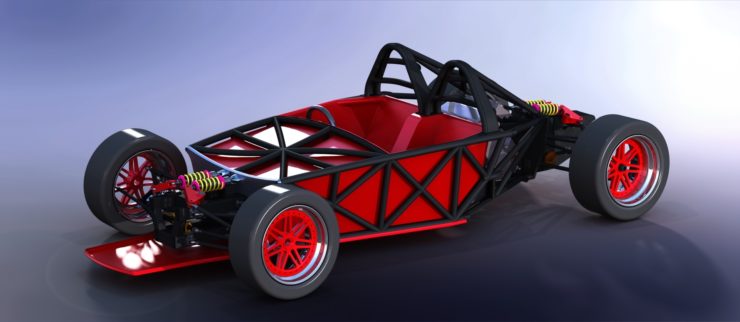
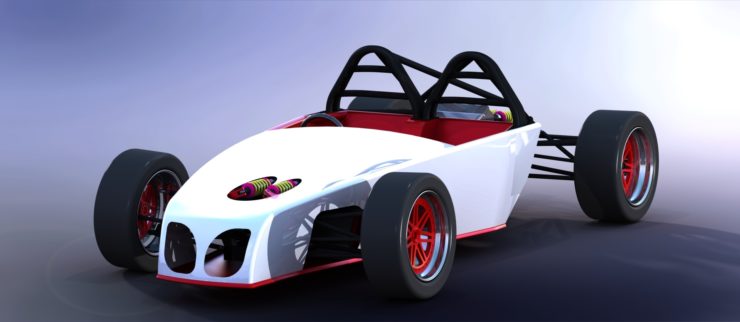